PIDKiln v0.9 (still) – second update
So this is a second update for current progress on building PIDKiln controller. This time it’s almost… almost finished 🙂
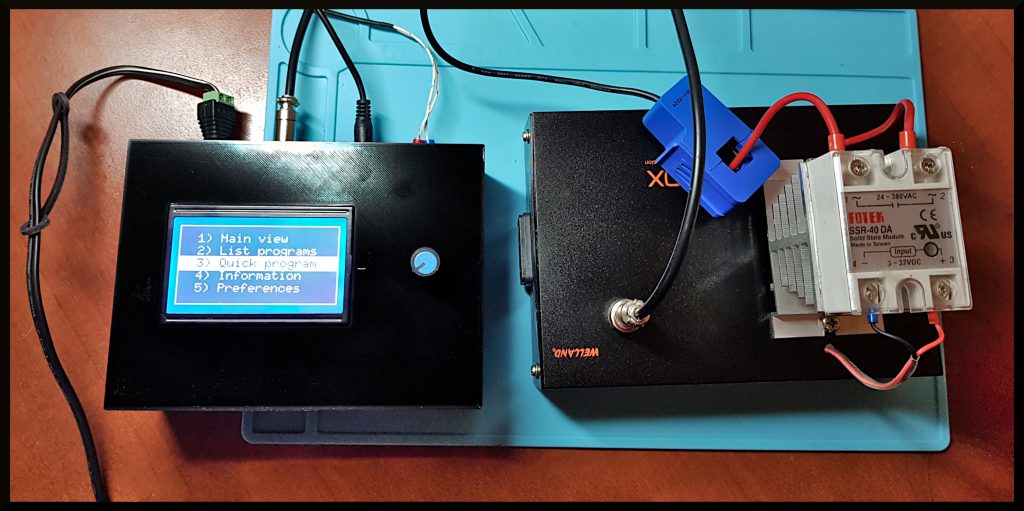
So this is a second update for current progress on building PIDKiln controller. This time it’s almost… almost finished 🙂
It’s time to make it look better, I don’t dare to say good :). So I’ve printed a case with all holes required, and now I’m soldering everything up.
I thought about creating dedicated PCB for it, but it probably would require double side one, and so far I’ve been only making one side PCB on my CNC mill. Other problem I’ve seen was the WiFi antenna on TTGO board. With single PCB for all components, It would be shielded either by PCB or LCD or wires. This board does not have external antenna connector (some other does). So I’ve decided I’ll put ESP32 board separately and at 90deg angle close to the plastic case. This way signal should be not blocked anyway. Continue Reading
So far so good – most of the stuff is done. Currently I’m tuning PID usage, and what’s left is traversing program in time – but that’s easy.
To tune PID parameters and test it, you can use simple halogen light bulb (or car light bulb) connected with thermocouple. This is a good heat source to around 100C and it’s easy to see when it’s working 🙂
You just have to switch SSR to DC-DC one (for kiln you probably will use DC-AC). For easy testing I’ve prepared “Quick program” in LCD menu – where you can set one program step. Provide desire temperature, time and dwell – and you can run it.
After some experience with controlling my ceramic kiln with Linux over cron scripts, I’ve moved to Chinese PC410 controller. But (probably) because it was knock off, it had removed plenty of useful features (you can read about it, in Polish here) I’ve decided to do my own controller.
I’ve looked around Internet for existing solutions, and found one – interesting enough, but still lacking very important future for me – Internet connectivity. I need to be able to monitor my kiln overt network, see what’s going on and be able to turn it off.
So this is how it came to life my controller – based on ESP32 chip, feature rich PID controller for kiln, with network connectivity, local LCD display and all possible safety features I needed.
You can download project sources from github and build your own. All required information you will find there. Here I’ll show how to build it in step-by-step process.
What’s done already (updated 19.09.2019):
What needs to be done:
Recent comments